Trusted by industry leaders for high-quality parts that reduce costs and boost efficiency across bottling, food, and more.
Efficient Maintenance Strategies for Krones Machinery in the Bottling Industry
1/3/20254 min read
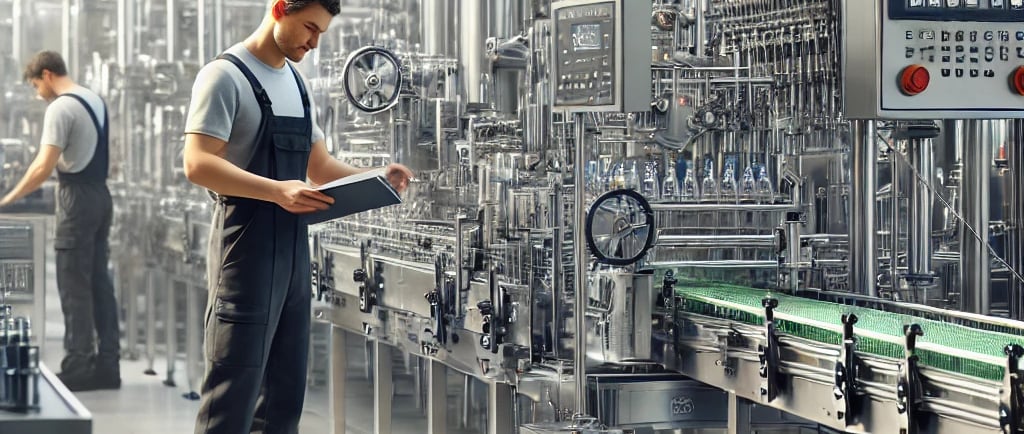
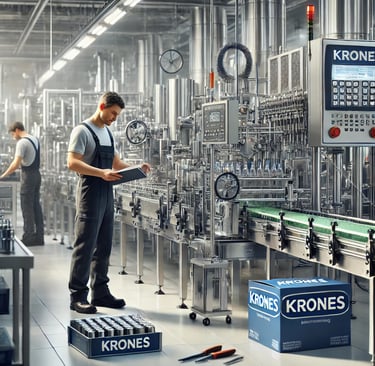
Key Maintenance Practices for Krones Machinery
To ensure the optimal performance of Krones machinery in the bottling industry, implementing key maintenance practices is imperative. Regular maintenance not only enhances the efficiency of the machines but also extends their lifespan. One of the primary practices is conducting routine inspections. These inspections should focus on identifying any signs of wear and tear, misalignments, or potential failures. It is advisable to create a checklist that includes all critical components of the machinery, such as motors, conveyor belts, and sensors, ensuring that no aspect is overlooked during the evaluation.
Another essential maintenance strategy involves adhering to specific cleaning protocols. Contaminants can adversely affect the performance of Krones machinery, leading to operational inefficiencies and potential health risks. Employing a systematic cleaning schedule that adheres to the manufacturer's guidelines will help maintain hygiene standards and machine functionality. This includes using appropriate cleaning agents and tools, especially in areas that come into contact with the products being processed.
Furthermore, establishing lubrication schedules is vital to the effective operation of the machinery. Lubrication reduces friction between moving parts, minimizing wear and tear. It is recommended to use high-quality lubricants specified for Krones machinery and to follow the manufacturer's instructions regarding lubrication frequency and application points. Additionally, it is crucial to monitor lubricant levels to ensure that they remain sufficient throughout the operational period.
Lastly, replacing worn-out parts before they lead to significant issues is a proactive maintenance practice. Regularly assessing the condition of components such as bearings, seals, and belts can prevent unexpected breakdowns. Keeping an inventory of critical spare parts assists in achieving swift replacements, thus mitigating downtime. By adhering to these key maintenance practices, operators can prevent costly disruptions and maximize the efficiency and longevity of Krones machinery.
Troubleshooting Common Issues
In the bottling industry, Krones machinery is essential for optimizing production efficiency. However, even the most reliable equipment can occasionally encounter issues that impede operations. Identifying and troubleshooting these common issues early can save time and costs. Some frequent problems include issues with conveyor belts, filling machines, or labeling equipment.
One common issue relates to conveyor belt malfunction. Symptoms may include unusual noises, slowed transport of bottles, or complete stoppage. These signs often indicate misalignment, wear and tear, or mechanical failure. To address these concerns, operators should first verify that the conveyor is correctly aligned and free of obstructions. Regular maintenance checks can also help in identifying components that require lubrication or replacement before they lead to severe operational disruptions.
Filling machine irregularities can also arise, such as inconsistent fill levels or spillage. Such issues can stem from blockages in the filling nozzles, air in the fluid lines, or variations in the bottle design affecting sensor calibration. Operators should systematically clean nozzles, check lines for air pockets, and calibrate sensors to ensure optimal performance. In cases where these actions do not rectify the problems, it may be necessary to consult the equipment’s technical manual or reach out to Krones support for further troubleshooting steps.
Labeling equipment might also experience issues. Bottles could be misaligned or labels may not adhesive properly. Troubleshooting should start by ensuring that the labeling device is set to the correct bottle size and that the adhesive is functioning optimally. Regular cleaning of labeling heads and inspection of spooling mechanisms can greatly reduce operational hitches.
While many issues can be handled in-house with a systematic approach and proper maintenance, certain complex problems—especially electrical or software-related failures—may necessitate professional intervention. It is crucial for operators to be trained to recognize when an issue has exceeded the scope of in-house repairs, thereby maintaining overall equipment efficiency and production uptime.
Implementing a Maintenance Plan and Monitoring Performance
Creating an effective maintenance plan for Krones machinery within the bottling industry is crucial to ensure optimal performance and longevity of the equipment. A structured maintenance strategy involves several key components, starting with the establishment of a comprehensive schedule. This schedule should outline routine checks and servicing intervals tailored to the specific needs of the machinery in use. By systematically planning maintenance activities, businesses can minimize unexpected downtimes and extend the operational lifespan of their equipment.
Tracking maintenance tasks is another vital aspect of a successful maintenance plan. It is essential to document all activities performed, including inspections, repairs, and replacements. Utilizing maintenance management software can greatly enhance this tracking process. This software allows for the detailed logging of maintenance activities, ensuring that no aspect of the machinery’s upkeep is overlooked. Furthermore, such documentation supports compliance with regulatory guidelines and helps in establishing a historical record that can be advantageous for future planning and audits.
Moreover, performance metrics play a significant role in assessing the efficiency of Krones machinery. Key performance indicators (KPIs) such as downtime, production output, and maintenance costs should be regularly monitored and analyzed. By evaluating these metrics, companies can identify trends, pinpoint areas that require improvement, and measure the effectiveness of their maintenance strategies over time. This data-driven approach not only facilitates proactive maintenance practices but also aids in optimizing overall production efficacy.
Regular monitoring and analysis constitute a feedback loop that drives continuous improvement. By being attentive to performance data and adjusting maintenance procedures accordingly, organizations can foster an environment of ongoing enhancement that benefits both the machinery and the overall production process. The commitment to implementing such strategies ensures that Krones machinery operates at its best, ultimately contributing to the success of bottling operations.
AMTIG Engineering Solutions
Tailored parts to enhance machinery performance.
© 2025. All rights reserved.
At AMTIG ENGINEERING SOLUTIONS LLC, we take pride in our innovative designs and technologies. Many of our products feature patented components, ensuring you receive the highest quality and unique performance. Our commitment to excellence is backed by our dedication to protecting our intellectual property.
*SIDEL, SBO, SERIES 1, SERIES 2, UNIVERSAL, MATRIX, EUROPA, LAGIRONDINE, ALSIM, COMBI are trademarks of SIDEL Inc. SIPA, SFR, ECS FX are trademarks of SIPA Plastic Packaging System S.p.A. KRONES, CONTIFORM are trademarks of KRONES GmbH. Zalkin is a trademark of ETS Andre Zalkin & Cie. Arol is a trademark of Arol s.p.a. CSI, ALCOA are trademarks of Closure Systems International. FOGG is a trademark of Fogg Filler Co.
AMTIG ENGINEERING Solutions LLC. is not a licensee of Sidel Inc., SIPA Plastic Packaging System S.p.A., KRONES GmbH, ETS Andre Zalkin & Cie, AROL s.p.a, Closure Systems International, or FOGG Filler Co. Additionally, AMTIG parts have not been approved or authorized by any of these companies.
+1(517) 292-2117
869 East Chicago RD, Suite #2 Quincy, MI