Trusted by industry leaders for high-quality parts that reduce costs and boost efficiency across bottling, food, and more.
Machining Standard Practice: A Guide to Precision and Efficiency
2/3/20252 min read
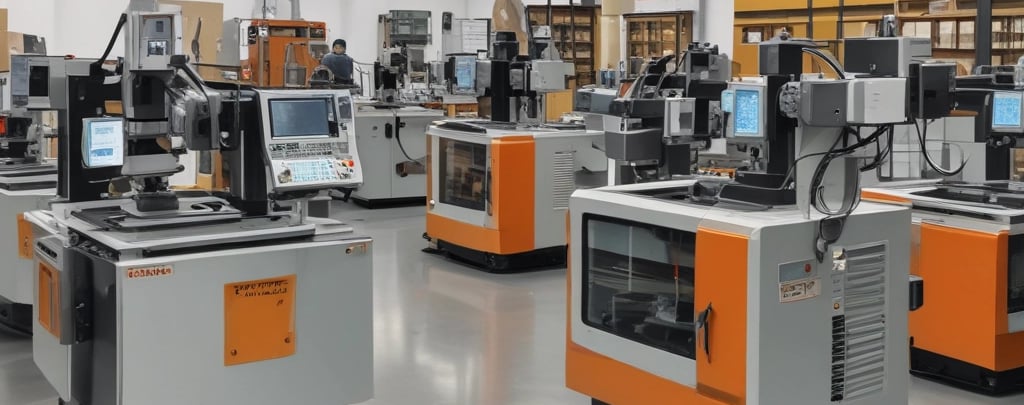
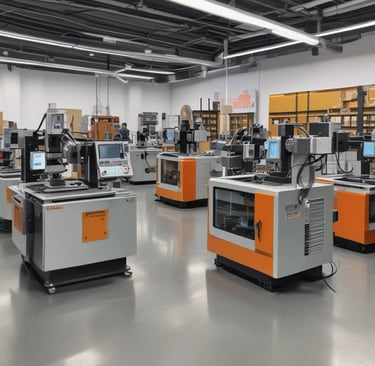
Machining is the backbone of modern manufacturing, requiring precision, consistency, and efficiency. Whether you're working with CNC machines or manual setups, adhering to machining standard practices ensures high-quality results, minimizes waste, and extends tool life. Mastering these principles leads to superior component quality, operational efficiency, and long-term cost savings.
1. Material Selection & Preparation
Choosing the right material is crucial for machining success. Factors such as hardness, thermal conductivity, machinability ratings, and intended application influence the machining approach. Proper preparation, including surface cleaning, stress relieving, and securing workpieces, reduces errors and enhances precision. Material defects or improper preparation can lead to premature tool wear and compromised product quality.
2. Tool Selection & Maintenance
Using the correct cutting tool for each operation ensures efficiency, productivity, and longevity. Tool geometry, coating, and material composition directly impact cutting performance. Regular inspections, proper storage, and timely sharpening or replacement of tools prevent unexpected downtime and maintain accuracy. Carbide, high-speed steel, and coated tools each have specific applications that optimize performance, and using the right toolholder further enhances stability.
3. Cutting Speeds & Feeds
Maintaining optimal speed and feed rates is critical to achieving superior results. Excessive speeds can cause tool wear, overheating, and surface finish defects, while slow speeds may reduce efficiency and increase cycle times. Consulting manufacturer recommendations and adjusting parameters based on material type, tooling, and machine rigidity enhance both productivity and surface quality. Balancing speed, depth of cut, and feed rate ensures smooth chip evacuation and reduces tool chatter.
4. Workholding & Fixturing
Secure workholding is fundamental to precision machining. Proper clamping, vises, fixtures, and jigs prevent vibrations, misalignment, and safety hazards. Advanced workholding techniques, such as vacuum chucks and magnetic fixturing, improve accessibility and machining accuracy. Ensuring that the workpiece remains stable throughout the operation minimizes dimensional variations and enhances repeatability in production.
5. Coolant & Lubrication
Heat is a major challenge in machining, affecting tool life and surface integrity. Using the right coolant or lubricant not only dissipates heat but also improves chip evacuation, enhances surface finish, and reduces friction. Flood cooling, mist cooling, and high-pressure coolant systems each serve specific applications. Selecting the appropriate fluid type prevents corrosion, reduces tool wear, and ensures compliance with environmental and safety regulations.
6. Quality Control & Inspection
Precision machining demands stringent quality checks at various stages of production. Employing tools such as micrometers, calipers, coordinate measuring machines (CMMs), laser scanners, and optical comparators helps detect deviations early. Statistical process control (SPC) techniques, in-process inspections, and final part verification reduce rework and ensure compliance with industry standards. Consistent quality control measures build trust with customers and enhance overall efficiency.
7. Safety & Best Practices
Adhering to safety protocols is vital to protecting machinists and equipment. Wearing proper personal protective equipment (PPE), such as safety glasses, gloves, and hearing protection, minimizes risks. Keeping workspaces clean, maintaining proper lighting, and following machine operating guidelines reduce accidents and operational errors. Automation and machine monitoring systems can further enhance safety and productivity.
Machining standard practices are the foundation of high-quality, efficient manufacturing. By implementing these principles, companies can achieve precision, reduce costs, and improve overall productivity. The key lies in continuous learning, adaptation, and a commitment to excellence in every machining process. Investing in skilled personnel, advanced technology, and robust quality control measures will further enhance operational success and competitiveness in the industry.
At AMTIG Engineering Solutions, we specialize in manufacturing high-quality precision parts to meet your needs. Whether you require custom components or large-scale production, our team is ready to deliver reliable solutions with top-tier machining expertise. Contact us today to discuss how we can support your manufacturing requirements.
AMTIG Engineering Solutions
Tailored parts to enhance machinery performance.
© 2025. All rights reserved.
At AMTIG ENGINEERING SOLUTIONS LLC, we take pride in our innovative designs and technologies. Many of our products feature patented components, ensuring you receive the highest quality and unique performance. Our commitment to excellence is backed by our dedication to protecting our intellectual property.
*SIDEL, SBO, SERIES 1, SERIES 2, UNIVERSAL, MATRIX, EUROPA, LAGIRONDINE, ALSIM, COMBI are trademarks of SIDEL Inc. SIPA, SFR, ECS FX are trademarks of SIPA Plastic Packaging System S.p.A. KRONES, CONTIFORM are trademarks of KRONES GmbH. Zalkin is a trademark of ETS Andre Zalkin & Cie. Arol is a trademark of Arol s.p.a. CSI, ALCOA are trademarks of Closure Systems International. FOGG is a trademark of Fogg Filler Co.
AMTIG ENGINEERING Solutions LLC. is not a licensee of Sidel Inc., SIPA Plastic Packaging System S.p.A., KRONES GmbH, ETS Andre Zalkin & Cie, AROL s.p.a, Closure Systems International, or FOGG Filler Co. Additionally, AMTIG parts have not been approved or authorized by any of these companies.
+1(517) 292-2117
869 East Chicago RD, Suite #2 Quincy, MI